We are living in a world where artificial intelligence (AI) is transforming eve....
What is the Most Important Requirement of Quality Management Systems?
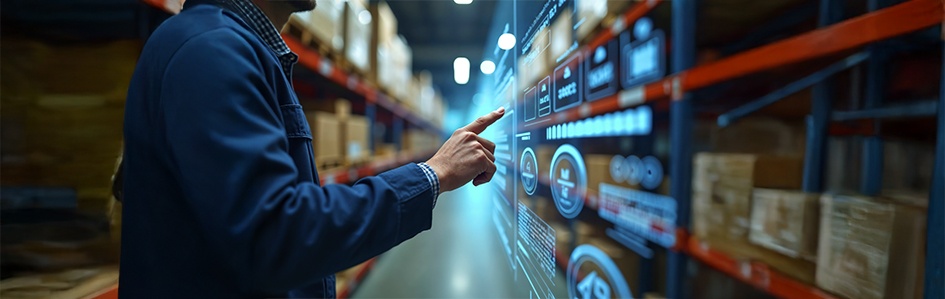
Before we begin, we want you to first imagine this scenario: Two companies decide to implement ISO 9001 at the same time. They use the same tools, work with the same consultants, and follow the same steps. But after a year, their results look very different. One company consistently meets customer expectations and improves its processes. The other faces repeated problems and low employee engagement.
What caused the difference?
It was not the standard itself or the documents they created. The key difference was leadership. In any Quality Management System - QMS, leadership commitment is not just helpful but essential for success.
What Is a Quality Management System?
A Quality Management System is a structured framework of policies, processes, and procedures that organizations use to ensure their products and services consistently meet customer and regulatory requirements. At its core, a QMS is not only about controlling quality but about managing it in a way that fosters continual improvement and strategic alignment.
The most widely recognized is ISO 9001, an international standard that provides a flexible yet robust set of requirements for establishing, implementing, maintaining, and continually improving a QMS. Rather than dictating specific actions, it allows organizations to adapt the standard to their unique operational and industry context.
ISO 9001 is based on seven key quality management principles, helping organizations improve efficiency and enhance customer satisfaction. Many people think it is only for large companies or manufacturers, but this is not true. The requirements of ISO 9001 are flexible and can be used by any organization, no matter its size, type, or what it offers.
How Is Leadership Demonstrated in a Quality Management System?
One of the most effective ways leadership commitment is demonstrated in a QMS is through management review. That is a structured process that ensures the system remains suitable, adequate, and effective in supporting organizational goals.
According to Mário Lavado, an experienced trainer and consultant in ISO standards, IT governance, and Lean Six Sigma:
“Management review should be approached as a process with clearly defined inputs, activities, and outputs. These include data from internal audits, stakeholder satisfaction, key performance indicators, and other quality-related metrics. The goal is to ensure strategic alignment, evaluate opportunities for improvement, and initiate necessary changes in a coordinated manner.”
Management review inputs typically involve:
- Results from audits and monitoring activities
- Feedback from customers and stakeholders
- Analysis of nonconformities, corrective actions, and process performance
- Status of actions from previous reviews
These inputs support informed decision-making. The outputs, as Mr. Lavado emphasizes, should include decisions on:
- Adjustments to quality objectives and resources
- Opportunities for process and system improvement
- Risk responses and corrective actions
- Revisions aligned with internal and external changes
He also highlights that risk-based thinking must be integrated into the review process to proactively address uncertainty and align the QMS with the organization's broader strategic direction.
“Management review must not be seen as a checklist exercise,” Mr. Lavado adds. “It should be integrated with the organization’s accountability cycle and driven by strategic intent, helping ensure that the QMS evolves in line with changing internal and external contexts.”
What Are the Benefits of a Quality Management System?
A Quality Management System offers many benefits by helping organizations improve the way they work, meet customer expectations, and achieve better results. It provides a clear structure for managing quality and helps teams stay focused on what matters most.
Studies show that certified organizations experience measurable benefits:
- An increase of over 20% in customer satisfaction, sales, process performance, and income compared to non-certified peers
- 98% of organizations report improved regulatory compliance, and ISO 9001– certified firms are 50% less likely to face regulatory sanctions
1. Improved Customer Satisfaction
ISO 9001 makes it easier for companies to keep customer satisfaction. It helps you set up clear processes and quality checks so that every customer gets the same good product or service every time.
2. Increased Operational Efficiency
One of the key advantages of a QMS is process standardization. When procedures are clearly defined and monitored, waste is reduced, bottlenecks are eliminated, and productivity increases. Organizations can do more with fewer resources.
3. Financial Benefits
A meta‑analysis of 42 studies confirmed ISO 9001 certification improves financial performance, boosting assets, sales, profitability, and market share.
4. Continual Improvement
A major benefit of a QMS is the focus on continual improvement. Through regular reviews, performance tracking, and feedback, organizations can make small, consistent changes that lead to long-term success.
5. Stronger Competitive Advantage
Companies with a certified QMS—especially ISO 9001—often stand out in the market. Certification increases credibility with customers, opens access to new markets, and may be a requirement for certain contracts or tenders.
How Can PECB Help You?
Whether you are just getting started with quality management or looking to advance your career, PECB offers internationally recognized ISO 9001 training courses designed to meet your professional goals.
Explore our ISO 9001 training course options below and choose the one that best suits your needs:
Learn the basics of ISO 9001 and how a Quality Management System works. This training course gives an easy-to-follow overview of the standard's requirements and how they apply in practice.
Gain the skills to set up, run, and improve a Quality Management System based on ISO 9001. This training course is great for those leading or supporting implementation projects.
Learn how to plan and carry out audits of Quality Management Systems. The training course covers key auditing practices to help ensure compliance with ISO 9001.
By becoming PECB certified, you demonstrate your commitment to quality, continual improvement, and professional excellence in line with globally recognized best practices.
About the Author
Albulena Veliu is a Marketing Copyeditor at PECB. She is responsible for refining and reviewing content to ensure clarity, consistency, and alignment with PECB’s editorial standards. For any questions, feel free to reach out to her at support@pecb.com.