We are living in a world where artificial intelligence (AI) is transforming eve....
Why Did Quality Become A Global Priority?
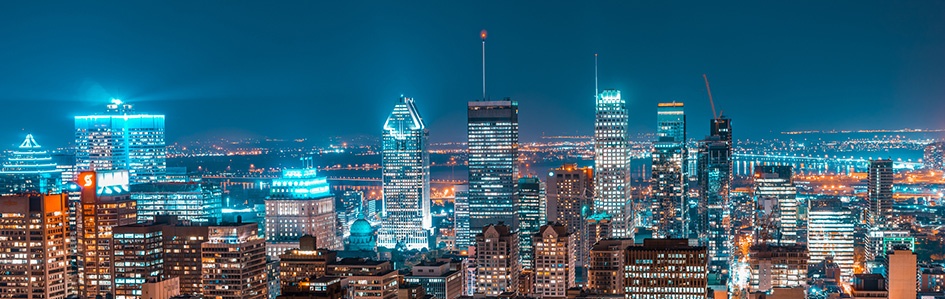
In today’s interconnected world, quality management has transcended borders and become a critical priority for organizations across industries. From manufacturing to service sectors, businesses recognize that delivering high-quality products and services is essential for survival and success. A study by the American Society for Quality (ASQ) reveals compelling findings: for every $1 invested in developing a QMS, businesses experienced a $6 increase in revenue, a $16 decrease in costs, and a $3 boost in profits. Moreover, the implementation of a QMS led to a 4.8% reduction in costs.
In this article, we will delve into the evolution of quality practices, their impact, and the benefits they bring.
A Brief History of Quality
Craft Guilds and Standards
Quality practices have a rich history dating back to the Middle Ages when Craft Guilds established standards to differentiate their goods. In medieval Europe, the Silversmith Guild set strict guidelines for silverware craftsmanship. Only items meeting these standards received the guild’s hallmark, ensuring quality for buyers.
The Industrial Revolution
The Industrial Revolution made quality control more prominent due to the rapid growth in the need for better quality products and increased competition. Since 1900, various tools, methodologies, standards, and frameworks have been established, forming the basics of quality management.
Japanese Influence
Throughout the 50s and 60s, Japan not only adopted quality methodologies from Western experts but also developed their own, significantly impacting global quality management practices.
- Kaizen: Developed by Japanese professionals, Kaizen emphasizes continuous improvement of processes within organizations. The philosophy soon became integral to quality management worldwide due to Japan’s success.
- Toyota Production System (TPS): Toyota’s TPS exemplifies the Kaizen principles. Through TPS, Toyota has empowered its employees to actively engage in the identification and resolution of quality issues, leading to significant improvements in efficiency.
The Japanese success brought crises to American organizations because they were offering higher quality products for lower prices. US companies managed to overcome the crises of the late 80s, early and 90s through quality initiatives. Quality tools and methodologies became major influences for businesses not only in the US, but also in Europe, Latin America, Asia, and the Middle East. US approach on quality involved a change in the entire organization, which soon came to be known as Total Quality Management. TQM emphasized continuous improvement, customer satisfaction, and employee involvement, revolutionizing how businesses approached quality.
Total Quality Management (TQM)
TQM has emerged as a comprehensive quality philosophy that encompasses every aspect of an organization, from processes to people. Globally, numerous companies have embraced TQM principles and integrated them into their operations, resulting in significant improvements in efficiency, cost reduction, and customer satisfaction.
Let us examine some prominent examples:
- Motorola’s Six Sigma: Motorola's adoption of Six Sigma principles stands as a testament to the transformative power of TQM. By implementing Six Sigma methodologies, Motorola achieved a remarkable 90% reduction in defects and realized savings of U.S. $17 billion between 1986 and 2001. Six Sigma became synonymous with quality excellence and played a pivotal role in enhancing Motorola's processes and products.
- Apple’s Product Quality: Apple's unwavering focus on TQM has been a cornerstone of its success in the technology industry. By upholding high standards in product design, manufacturing, and customer service, Apple has cultivated a reputation for innovation and quality. Key metrics, such as consistently exceeding 82% in customer satisfaction ratings and maintaining significantly lower product return rates compared to industry averages, underscore Apple's commitment to robust quality control. Furthermore, Apple's relentless pursuit of continuous improvement has fueled consistent year-over-year growth in product performance and customer loyalty.
- Toyota’s Lean Manufacturing: Toyota's embrace of Total Quality Management (TQM) and lean manufacturing principles, epitomized by the Toyota Production System (TPS), has yielded remarkable results. Achievements include a 12% reduction in production costs, decreasing vehicle defects to less than 0.7 per 10,000 vehicles, and realizing an annual productivity growth of 9%. These milestones underscore Toyota's commitment to operational excellence and the efficacy of TQM in driving continuous improvement.
By adopting TQM practices, these industry leaders have not only enhanced their operational efficiency and reduced costs but have also maintained exceptional levels of customer satisfaction. Their commitment to quality excellence has solidified their positions as global leaders in their respective industries, serving as compelling examples of the widespread adoption and success of TQM principles on a global scale.
ISO Standards and Globalization
From the late 90s onwards, quality management practices became common across both manufacturing and service industries. The International Organization for Standardization (ISO) published standards that are widely used globally.
ISO 9001 Quality Management System
A widely adopted Quality Management System (QMS) standard that ensures consistent quality practices across organizations.
This standard provides a structured framework for organizations to establish, implement, maintain, and continually improve their quality management systems. By emphasizing process improvement, customer focus, and continuous learning, ISO 9001 helps organizations build robust quality management systems that serve as the foundation for excellence and innovation.
Impact of Current Trends and Advanced Technologies on Quality Management
In addition to established quality management practices and standards like ISO 9001, the evolution of technology has brought about transformative changes in how organizations approach quality assurance. Here are some key ways in which current trends and advanced technologies have influenced quality management:
- Data Analytics: Using tools to analyze big data helps companies understand processes and spot trends for better quality control.
- Internet of Things (IoT): Connected devices allow real-time monitoring of production and products, catching quality issues early.
- Artificial Intelligence (AI) and Machine Learning (ML): AI predicts defects and helps optimize quality processes, making inspections more accurate.
- Automation and Robotics: Machines can perform tasks precisely and consistently, improving quality in manufacturing.
- Blockchain Technology: This technology ensures the authenticity of products throughout the supply chain, boosting trust in quality.
- Augmented Reality (AR) and Virtual Reality (VR): These technologies enhance training and make quality inspections more effective by creating immersive experiences.
- Digital Twins: Virtual replicas of processes help companies monitor and optimize quality in real-time.
By embracing these current trends and advanced technologies, organizations can enhance their quality management practices, drive operational efficiency, and deliver superior products and services that meet or exceed customer expectations.
Benefits of Quality Management
Quality management brings numerous benefits, including:
Conclusion
Implementing quality management is essential, not optional. Organizations that prioritize quality remain competitive, adapt to change, and thrive in the global marketplace. As we continue to evolve, let us embrace quality as a shared responsibility—one that transcends borders and drives excellence.
How Can PECB Help?
PECB provides ISO 9001 Quality Management System training courses and certification services for professionals aiming to gain comprehensive knowledge of quality management principles, core subjects, and issues. The training courses are suitable for quality professionals, project managers, and consultants supporting the integration of quality management systems within an organization. Additionally, ISO 9001 training is valuable for auditors conducting and leading quality management certification audits and staff involved in implementing the ISO 9001 standard.
ISO 9001 Training Courses by PECB:
- Certified ISO 9001 Lead Auditor: Comprehensive training for leading quality management audits.
- Certified ISO 9001 Lead Implementer: Training focused on implementing ISO 9001 standards within organizations.
- Certified ISO 9001 Foundation: Basic training on quality management principles.
Six Sigma
Six Sigma is a method that focuses on improving quality by identifying and eliminating defects in processes. It uses data and statistical tools to analyze and enhance workflows, leading to greater efficiency and customer satisfaction. Six Sigma employs a structured approach known as DMAIC (Define, Measure, Analyze, Improve, and Control) to achieve these goals.
Six Sigma Belts:
- Six Sigma Yellow Belt: Basic understanding of Six Sigma principles and practices, suitable for team members who support improvement projects.
- Six Sigma Green Belt: Intermediate level of Six Sigma training, allowing individuals to lead small-scale projects and assist Black Belts in larger initiatives.
About the Author
Teuta Hyseni is the Senior Web Content Specialist at PECB. She is responsible for updating and managing website content. If you have any questions, please do not hesitate to contact: support@pecb.com